What is Porosity in Welding: Finest Practices for Avoiding Porous Welds
What is Porosity in Welding: Finest Practices for Avoiding Porous Welds
Blog Article
The Science Behind Porosity: A Comprehensive Guide for Welders and Fabricators
Recognizing the detailed devices behind porosity in welding is essential for welders and makers aiming for impressive craftsmanship. From the make-up of the base materials to the complexities of the welding procedure itself, a wide variety of variables conspire to either aggravate or alleviate the existence of porosity.
Recognizing Porosity in Welding
FIRST SENTENCE:
Evaluation of porosity in welding discloses important insights right into the integrity and high quality of the weld joint. Porosity, characterized by the existence of tooth cavities or gaps within the weld steel, is a common issue in welding processes. These spaces, otherwise appropriately resolved, can jeopardize the architectural honesty and mechanical residential or commercial properties of the weld, resulting in possible failures in the finished item.
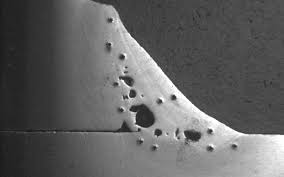
To discover and quantify porosity, non-destructive testing techniques such as ultrasonic testing or X-ray examination are typically utilized. These strategies permit for the identification of interior problems without endangering the integrity of the weld. By assessing the size, form, and circulation of porosity within a weld, welders can make informed choices to boost their welding processes and attain sounder weld joints.
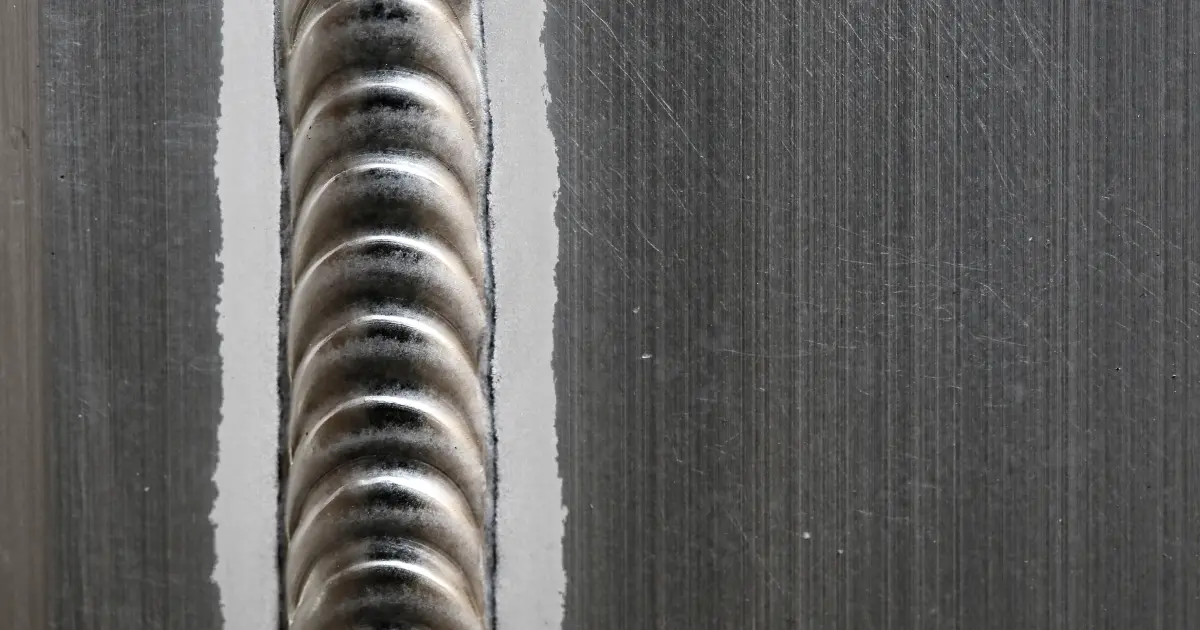
Aspects Affecting Porosity Development
The occurrence of porosity in welding is influenced by a myriad of factors, varying from gas protecting performance to the details of welding specification settings. Welding specifications, consisting of voltage, present, travel rate, and electrode kind, also impact porosity formation. The welding method employed, such as gas steel arc welding (GMAW) or shielded steel arc welding (SMAW), can influence porosity formation due to variations in warm circulation and gas protection - What is Porosity.
Effects of Porosity on Weld Top Quality
Porosity formation dramatically endangers the architectural honesty and mechanical residential properties of bonded joints. When porosity is present in a weld, it develops spaces or tooth cavities within the product, lowering the overall toughness of the joint. These voids act as anxiety focus factors, making the weld extra susceptible to fracturing and failure under load. The presence of porosity likewise compromises the weld's resistance to corrosion, home as the trapped air or gases within deep spaces can react with the surrounding atmosphere, leading to destruction over time. Furthermore, porosity can prevent the weld's capacity to endure pressure or influence, more endangering the overall high quality and integrity of the welded framework. In critical applications such as aerospace, auto, or structural constructions, where security and toughness are extremely important, the harmful impacts of porosity on weld top quality can have severe effects, highlighting the relevance of reducing porosity through proper welding techniques and treatments.
Techniques to Reduce Porosity
To improve the high quality of bonded joints and guarantee architectural stability, welders and makers employ certain methods targeted at decreasing the development of spaces and cavities within the product during the welding procedure. One reliable method to reduce porosity is to make sure correct material preparation. This includes detailed cleaning of the base metal to remove any kind of contaminants such as oil, grease, or moisture that could contribute to porosity development. Additionally, using the suitable welding criteria, such as the right voltage, current, and take a trip rate, is vital in protecting against porosity. Maintaining a constant arc size and angle throughout welding additionally helps minimize the possibility of porosity.

In addition, picking the appropriate protecting gas and maintaining appropriate gas flow rates are vital in lessening porosity. Utilizing the proper welding method, such look at this now as back-stepping or employing a weaving movement, can additionally help distribute warmth evenly and decrease the chances of porosity formation. Last but not least, ensuring appropriate air flow in the welding atmosphere to remove any type of potential resources of contamination is vital for attaining porosity-free welds. By executing these techniques, welders can properly reduce porosity and generate top quality welded joints.

Advanced Solutions for Porosity Control
Applying cutting-edge innovations and ingenious techniques plays an essential function in achieving remarkable control over porosity in welding procedures. One advanced solution is using innovative gas combinations. Securing gases like helium or a blend of argon and hydrogen can help in reducing porosity by providing better arc stability and boosted gas coverage. In addition, using innovative welding techniques such as pulsed MIG welding or modified ambience welding can also aid minimize porosity problems.
An additional sophisticated solution involves the use of sophisticated welding tools. For example, making use of devices with built-in attributes like waveform control and sophisticated power resources can enhance weld top quality and lower porosity dangers. Additionally, the application of automated welding systems with precise control over parameters can substantially minimize porosity flaws.
Moreover, integrating sophisticated surveillance and inspection modern technologies such as real-time X-ray Source imaging or automated ultrasonic screening can assist in spotting porosity early in the welding process, enabling immediate rehabilitative actions. In general, incorporating these sophisticated services can greatly enhance porosity control and improve the general high quality of bonded parts.
Conclusion
To conclude, recognizing the scientific research behind porosity in welding is necessary for welders and makers to generate high-grade welds. By recognizing the factors affecting porosity development and executing techniques to reduce it, welders can boost the general weld high quality. Advanced solutions for porosity control can further boost the welding process and make sure a strong and reliable weld. It is necessary for welders to continuously educate themselves on porosity and carry out best methods to attain optimal outcomes.
Report this page